- Chemical Engineering Basics - Section 1
- Chemical Engineering Basics - Section 2
- Chemical Engineering Basics - Section 3
- Chemical Engineering Basics - Section 4
- Chemical Engineering Basics - Section 5
- Chemical Engineering Basics - Section 6
- Chemical Engineering Basics - Section 7
- Chemical Engineering Basics - Section 8
- Chemical Engineering Basics - Section 9
- Chemical Engineering Basics - Section 10
- Chemical Engineering Basics - Section 11
- Chemical Engineering Basics - Section 12
- Chemical Engineering Basics - Section 13
- Chemical Engineering Basics - Section 14
- Chemical Engineering Basics - Section 15
- Chemical Engineering Basics - Section 16
- Chemical Engineering Basics - Section 17
- Chemical Engineering Basics - Section 18
- Chemical Engineering Basics - Section 19
- Chemical Engineering Basics - Section 20
- Chemical Engineering Basics - Section 21
- Chemical Engineering Basics - Section 22
- Chemical Engineering Basics - Section 23
- Chemical Engineering Basics - Section 24
- Chemical Engineering Basics - Section 25
- Chemical Engineering Basics - Section 26
- Chemical Engineering Basics - Section 27
- Chemical Engineering Basics - Section 28

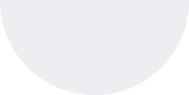
Chemical Engineering Basics - Engineering
Q1: __________ is not a case hardening process.A Carburising
B Nitriding
C Cyaniding
D Annealing
ANS:A - Carburising Carburizing is a case-hardening process used to increase the surface hardness of low-carbon steels or iron-based alloys. The process involves introducing carbon into the surface layer of the material to create a hardened outer shell while maintaining a relatively softer and more ductile core. This is achieved by exposing the material to a carbon-rich environment at elevated temperatures. The typical steps involved in carburizing are as follows:
|
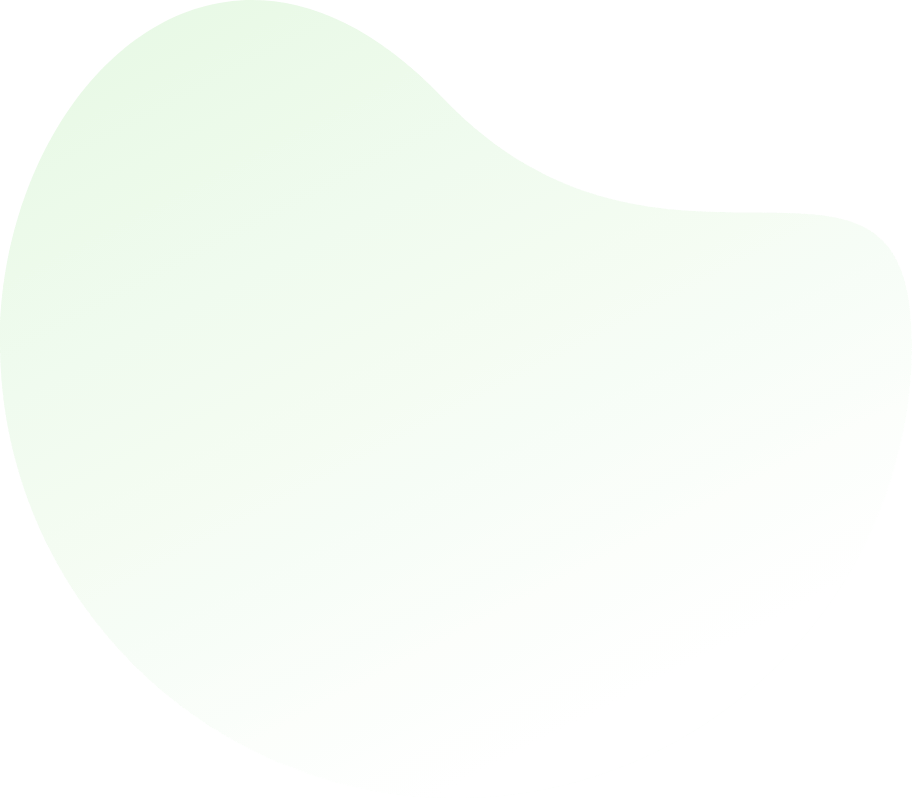
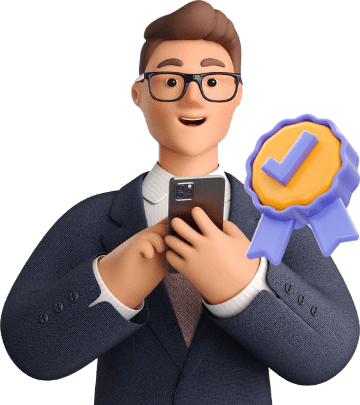
For help Students Orientation
Mcqs Questions
One stop destination for examination, preparation, recruitment, and more. Specially designed online test to solve all your preparation worries. Go wherever you want to and practice whenever you want, using the online test platform.