- Chemical Engineering Basics - Section 1
- Chemical Engineering Basics - Section 2
- Chemical Engineering Basics - Section 3
- Chemical Engineering Basics - Section 4
- Chemical Engineering Basics - Section 5
- Chemical Engineering Basics - Section 6
- Chemical Engineering Basics - Section 7
- Chemical Engineering Basics - Section 8
- Chemical Engineering Basics - Section 9
- Chemical Engineering Basics - Section 10
- Chemical Engineering Basics - Section 11
- Chemical Engineering Basics - Section 12
- Chemical Engineering Basics - Section 13
- Chemical Engineering Basics - Section 14
- Chemical Engineering Basics - Section 15
- Chemical Engineering Basics - Section 16
- Chemical Engineering Basics - Section 17
- Chemical Engineering Basics - Section 18
- Chemical Engineering Basics - Section 19
- Chemical Engineering Basics - Section 20
- Chemical Engineering Basics - Section 21
- Chemical Engineering Basics - Section 22
- Chemical Engineering Basics - Section 23
- Chemical Engineering Basics - Section 24
- Chemical Engineering Basics - Section 25
- Chemical Engineering Basics - Section 26
- Chemical Engineering Basics - Section 27
- Chemical Engineering Basics - Section 28

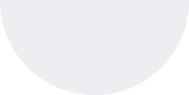
Chemical Engineering Basics - Engineering
Q1: By X-ray diffraction, it is not possible to determine theA preferred orientation.
B residual localised stresses.
C particle size.
D ordered arrangement of magnetic moments.
ANS:B - residual localised stresses. Residual localized stresses, also known as residual stresses or residual strain, are internal stresses that remain in a material even after external loads or forces have been removed. These stresses can occur during manufacturing, processing, or assembly processes and can have significant effects on the performance and behavior of materials and components. Here's an explanation of residual localized stresses:
|
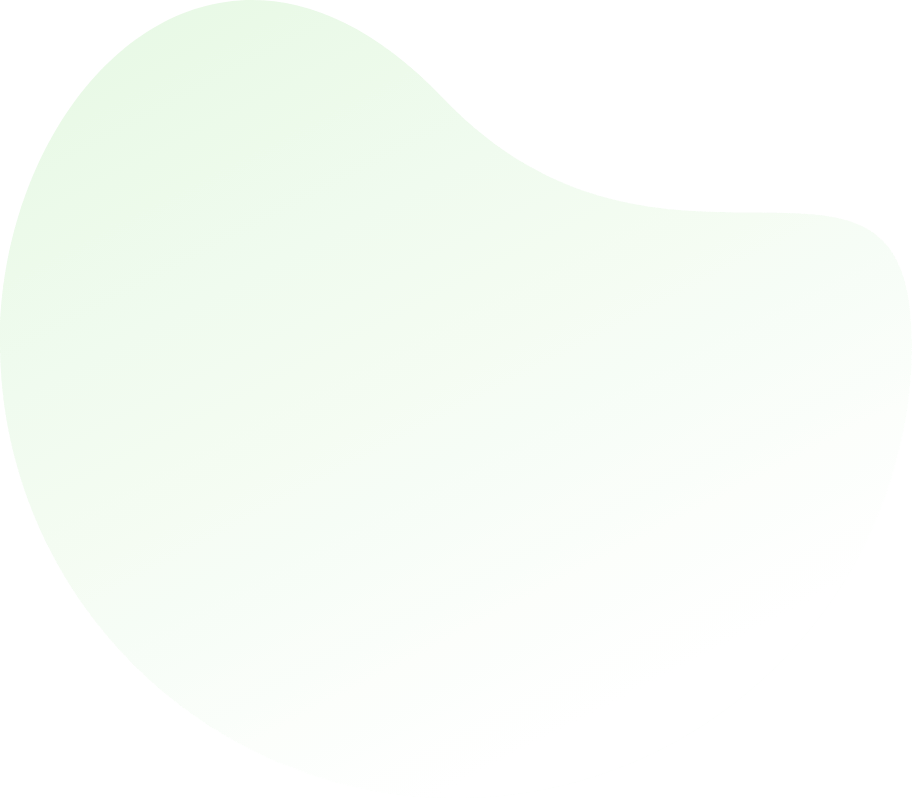
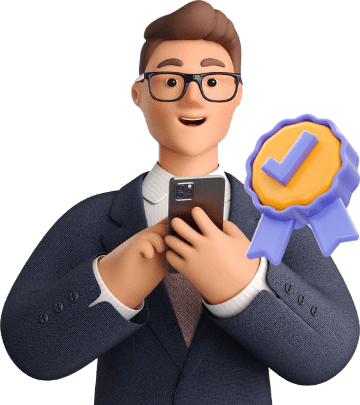
For help Students Orientation
Mcqs Questions
One stop destination for examination, preparation, recruitment, and more. Specially designed online test to solve all your preparation worries. Go wherever you want to and practice whenever you want, using the online test platform.