- Chemical Engineering Basics - Section 1
- Chemical Engineering Basics - Section 2
- Chemical Engineering Basics - Section 3
- Chemical Engineering Basics - Section 4
- Chemical Engineering Basics - Section 5
- Chemical Engineering Basics - Section 6
- Chemical Engineering Basics - Section 7
- Chemical Engineering Basics - Section 8
- Chemical Engineering Basics - Section 9
- Chemical Engineering Basics - Section 10
- Chemical Engineering Basics - Section 11
- Chemical Engineering Basics - Section 12
- Chemical Engineering Basics - Section 13
- Chemical Engineering Basics - Section 14
- Chemical Engineering Basics - Section 15
- Chemical Engineering Basics - Section 16
- Chemical Engineering Basics - Section 17
- Chemical Engineering Basics - Section 18
- Chemical Engineering Basics - Section 19
- Chemical Engineering Basics - Section 20
- Chemical Engineering Basics - Section 21
- Chemical Engineering Basics - Section 22
- Chemical Engineering Basics - Section 23
- Chemical Engineering Basics - Section 24
- Chemical Engineering Basics - Section 25
- Chemical Engineering Basics - Section 26
- Chemical Engineering Basics - Section 27
- Chemical Engineering Basics - Section 28

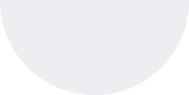
Chemical Engineering Basics - Engineering
Q1: In a casting, cold shut defect is caused byA low pounhg temperature.
B melt-mould reactions.
C faulty gating system.
D very low mould permeability.
ANS:A - low pounhg temperature. Cold shut defect in casting occurs when two portions of metal flow together during solidification but fail to fuse properly due to insufficient fluidity or inadequate pouring temperature. The correct cause of cold shut defect is low pouring temperature. When the pouring temperature of the molten metal is too low, it solidifies rapidly upon contact with the cooler mold surfaces or previously solidified metal, leading to incomplete fusion between the two streams of metal. This results in a visible seam or line along the casting surface, known as a cold shut defect. The low pouring temperature prevents the molten metal from properly filling the mold cavity and merging together, resulting in the formation of a discontinuity in the casting. Cold shut defects can weaken the casting and compromise its structural integrity, making them undesirable in most casting applications. While other factors such as faulty gating systems, melt-mold reactions, or low mold permeability can contribute to casting defects, they do not directly cause cold shut defects. Therefore, the correct cause of cold shut defect is low pouring temperature. |
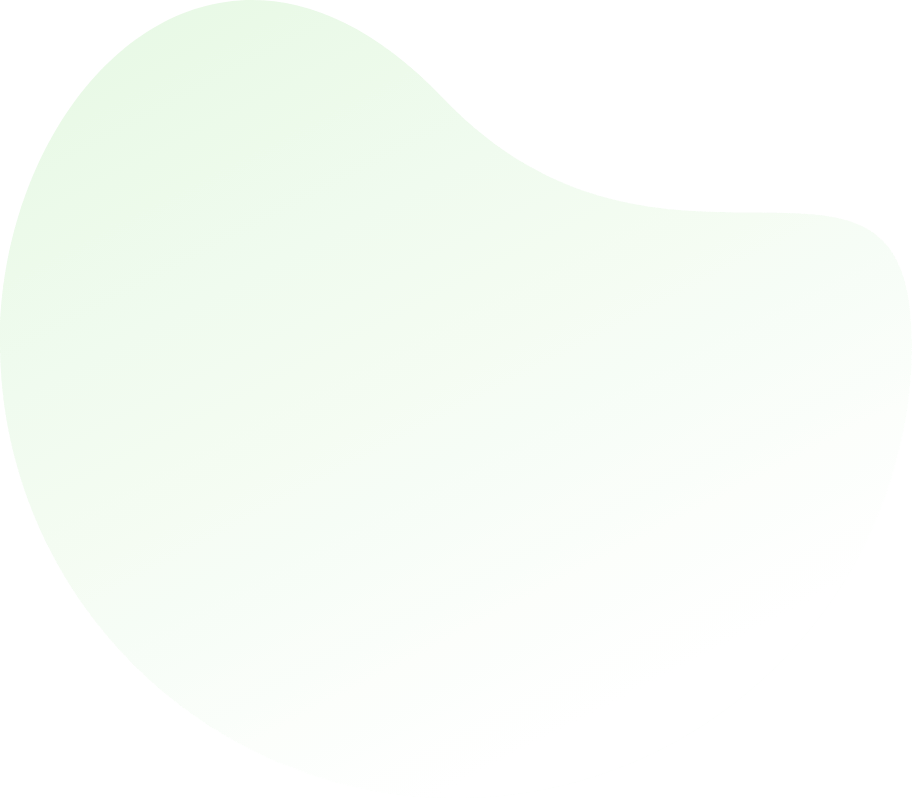
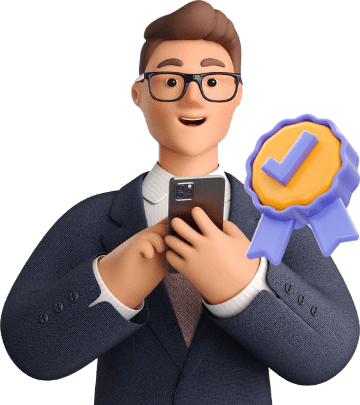
For help Students Orientation
Mcqs Questions
One stop destination for examination, preparation, recruitment, and more. Specially designed online test to solve all your preparation worries. Go wherever you want to and practice whenever you want, using the online test platform.