- Chemical Engineering Basics - Section 1
- Chemical Engineering Basics - Section 2
- Chemical Engineering Basics - Section 3
- Chemical Engineering Basics - Section 4
- Chemical Engineering Basics - Section 5
- Chemical Engineering Basics - Section 6
- Chemical Engineering Basics - Section 7
- Chemical Engineering Basics - Section 8
- Chemical Engineering Basics - Section 9
- Chemical Engineering Basics - Section 10
- Chemical Engineering Basics - Section 11
- Chemical Engineering Basics - Section 12
- Chemical Engineering Basics - Section 13
- Chemical Engineering Basics - Section 14
- Chemical Engineering Basics - Section 15
- Chemical Engineering Basics - Section 16
- Chemical Engineering Basics - Section 17
- Chemical Engineering Basics - Section 18
- Chemical Engineering Basics - Section 19
- Chemical Engineering Basics - Section 20
- Chemical Engineering Basics - Section 21
- Chemical Engineering Basics - Section 22
- Chemical Engineering Basics - Section 23
- Chemical Engineering Basics - Section 24
- Chemical Engineering Basics - Section 25
- Chemical Engineering Basics - Section 26
- Chemical Engineering Basics - Section 27
- Chemical Engineering Basics - Section 28

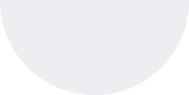
Chemical Engineering Basics - Engineering
Q1: Use of flux during soldering is done toA increase flidity of solder by lowering its melting temperature.
B prevent oxide formation.
C wash away surplus solder.
D full up the joint gap.
ANS:B - prevent oxide formation. The use of flux during soldering is primarily done to prevent oxide formation. Flux serves several purposes in the soldering process, but its primary function is to clean and prepare the surfaces to be soldered by removing oxides and contaminants. Oxides can form on the surface of metals being soldered due to exposure to air or other environmental factors, and these oxides can inhibit the formation of a strong bond between the solder and the metal surfaces. Here are some key functions of flux in soldering:
|
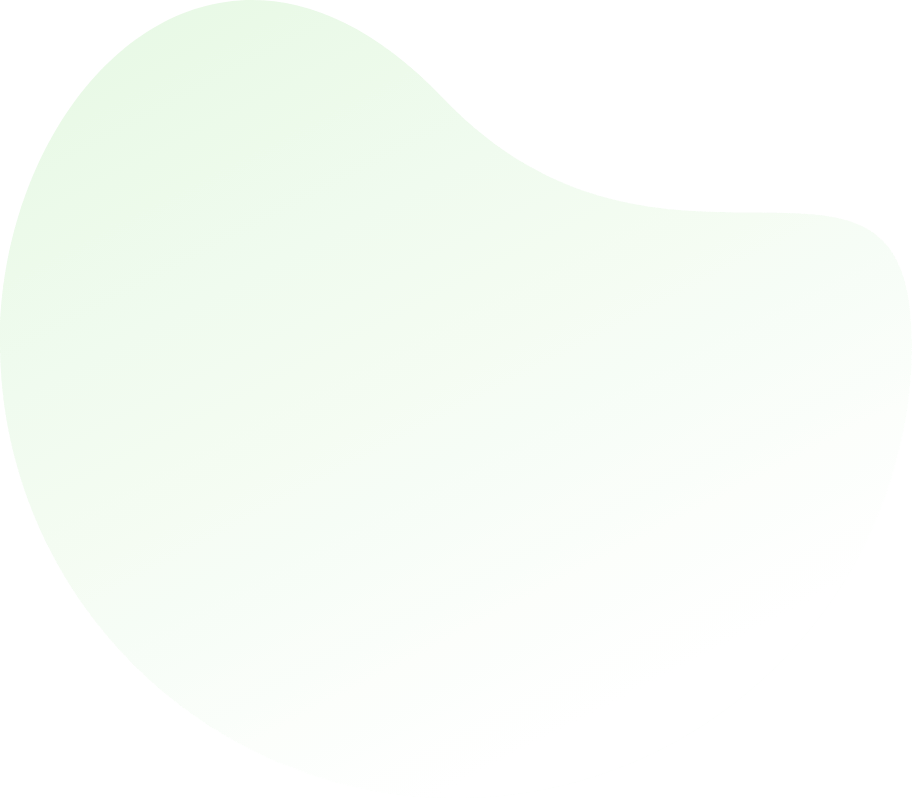
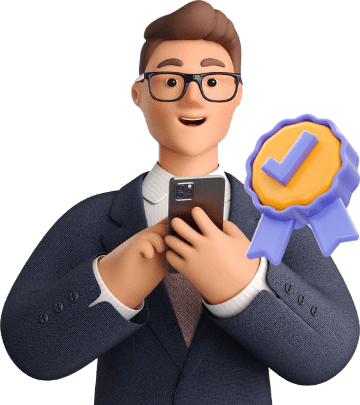
For help Students Orientation
Mcqs Questions
One stop destination for examination, preparation, recruitment, and more. Specially designed online test to solve all your preparation worries. Go wherever you want to and practice whenever you want, using the online test platform.